Interview met CEO Roberto Salmini
To learn more about the motivations and needs that led the Italian company Lazzati, winner of the Oro Process Innovator award, to trust Logica for their process management, Logica interviewed Roberto Salmini, CEO of the company.

Here for the non-Italian readers, it’s important to mention Lazzati is a long-lasting user of the Italian MIS “Proto”. The mentioned module Job Calendar is part of Proto, while quality check module is art of GPC MES, which is the shop floor data collection and OEE monitoring system from Logica, which is open for integration with any existing third-party MIS/ERP.
Roberto:
I start right from prehistory.
My father was very meticulous. Unlike other printers who just made estimates, he also took care of making the final statements.
When I joined the company in 1982 at 19, I inherited the same task of verifying calculations. But over time that job became tedious and sometimes boring.
I remember looking at IBM MIS solutions when I saw Proto and thought, “I’ll buy it.”
At first, we only used it for estimates, but soon we integrated all its modules, including automated data collection, which my father was doing, also, manually. The philosophy was the same: why waste hours entering data manually when automation could do it?
David Triulzi from Logica:
So we could say the attitude toward solutions like Data Production came from a mindset, firstly from your father and then from you.
R: That’s right, it all started with my father’s approach, which I then transferred to IT.
There has always been a need to improve and optimize processes, and this has led us to have, for more than 20 years, the entire production process under control.
The first big difference we found was in efficiency: before, employees tended to “balance” the eight hours, showing an apparent efficiency of 95%.
Then with automated collection, we dropped to 80%.
D: It was quite a natural transition for you, but how has this transformation impacted on employees?
R: I admit that at first the impact was significant.
Initially it felt like a control tool. Also, on machines it’s quite simple to use but manual one, for example in packaging where there are many different items and types of processes, is more complex.
Plus, we’re a company with a wide range of publishing and converting outputs that deals with heterogeneous personnel: some more inclined toward IT tools and find them easier to handle, others less so.
We’ve also emphasized the importance of properly justifying unproductive time.
Over the years we’ve made three business acquisitions.
The first and second had no IT system at all, while the third used Proto but didn’t yet have a MES. This is because, in 90% of cases, small to medium-sized companies use only the estimate module, at most the job order and, in rare cases, the final report. Employees were still used to the old methods, but it’s a small hurdle that is easily solved in a month by teaching newcomers how to use the software.
D: Have they understood the mindset of the company, your needs and the reasons why you use these tools?
R: Yes! Today it’s a shared project, and as we go along, we’re reinforcing the importance of reliable data.
We feel it would be impossible to run the company without complete software like yours.
D: You lead me to an off-track question. Can you explain this last concept?
R: In my opinion, the biggest challenge is production scheduling.
Without accurate estimates, timely job management and tools like Logica’s Job Calendar, which makes the status and placement of jobs visible to the entire company, it becomes impossible.
So everything is fully integrated. In an environment where conflicts over priorities are inevitable, especially during periods of saturation, software that centralizes information enables more informed and data-driven decisions.
D: What has been the ROI in using Logica Suite?
R: Today we must manage multi-sector experiences, from converting to publishing, and the complexity and speed of requests have increased.
Beyond staff savings, there is much more than that. Logica has always distinguished by being open to dialogue with other systems to provide a service that is comprehensive and gives more peace of mind to the customer and is not, on the other hand, “protectionist.”
In this sense I address great appreciation towards Andrea Sentimenti who is, in my opinion, a key figure in Logica.
This is by no means a given. The client is in any case integrated with Logica Suite and, therefore, with us. This exceeds what Logica normally offers and is a remarkable added value.
D: Logica has recently supported you with consulting activities. What benefits are you gaining from this?
R: Last year, with Norberto and Serena, another very skilled and helpful Logica team figure, we analyzed logistics flows. The goal was to improve the understanding of these aspects and overall efficiency, which had already increased by 4-5%. It’s more of a cultural change in the company: moving from a management based on “feelings” to one based on concrete data.
Side-by-side activities with a focus on validation lead also to more focused strategic choices: for example, investing in new equipment or recognizing our strengths and focusing on them.
And the positive impact is also reflected in planning which is more reliable and accurate.
D: Is this something that has been extended to your staff as well? How has it been responded to?
R: It is quite extended.
We hold regular meetings with different goals: weekly dedicated to the Job Calendar; monthly on quality, to identify inefficiencies and plan improvements; and ad hoc sessions with specific departments.
The team has welcomed these initiatives with interest and participation.
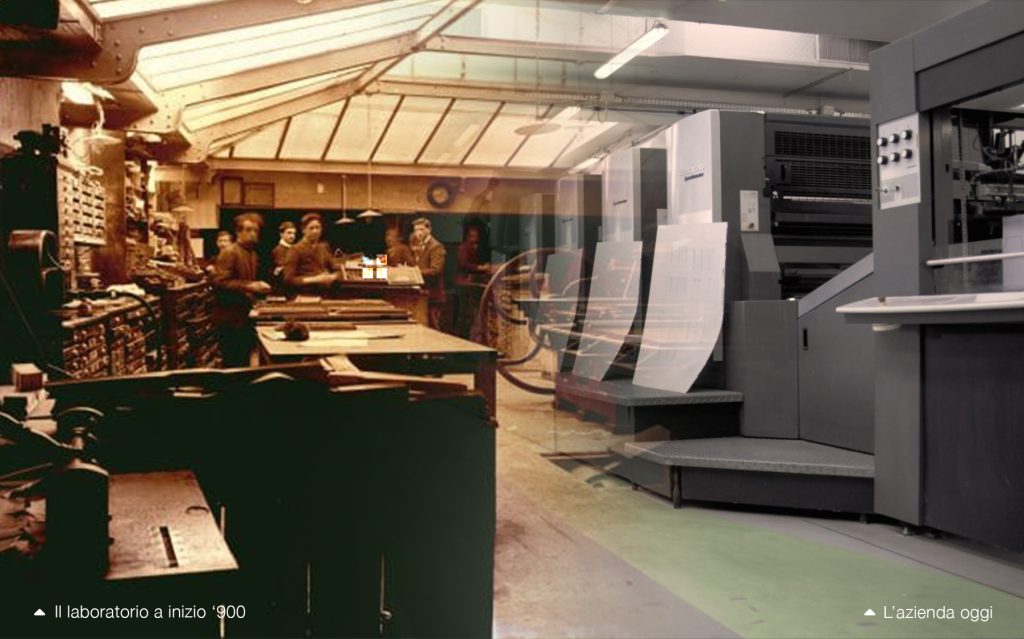
D: Lazzati stands out for its long experience as your sister recalled “a company with 220 years of history.” In this time, you have faced generational transitions and built the foundation for the future. How does Logica in that sense provide you with continuity?
R: When I joined the company, we were just a few people with my father centralizing all the activities, as happens in most traditional printing companies.
My goal was to create a structure that could function independently. My role remains important, but it is essential that there is a solid structure that can carry on with the business even in my absence.
To achieve this, it has been essential to have software that has become the organizational pillar on which business processes are based and the presence of key figures to pass on the company’s heritage to new generations.
D: Your company also operates in the luxury segment with a demanding and high-level customer. What’s Logica’s contribution to maintaining high quality standards in line with expectations?
R: One of the most useful tools we’ve integrated is the quality check module that, at regular copy intervals, allows us to certify product quality and work to improve them. This is a significant first step.
The second one, which we plan to activate early, will be even more advanced: it will allow us to photograph the product and visually certify the quality standard, identifying any non-conformities and their causes.
The added value isn’t directly reflected on the customer but translates into vital support for the overall business processes management.
I always tend to reassure our clients that we manage the entire business with software that covers every aspect, from A to Z.

D: Your project presented at Oro della Stampa (Gold of the Printing) event received an award for innovation. What contributed to this success?
R: I think everything we accomplished with Logica weighed a good 80%.
We have innovated so much, not only in the IT aspect, but also in the machines, and I think all this testifies how much we pay attention to the most advanced solutions.
D: In conclusion, if you should speak to someone who hasn’t embarked on a path like yours, what message would you give?
R: Start immediately.
Over the years, I’ve had visits from other companies interested in seeing how your software works in the field, and I’ve always spoken very positively about it. I know that one company, which won another Oro della Stampa award, installed the system last year, starting from zero, and I’m glad to think that our input was helpful on their journey as well.